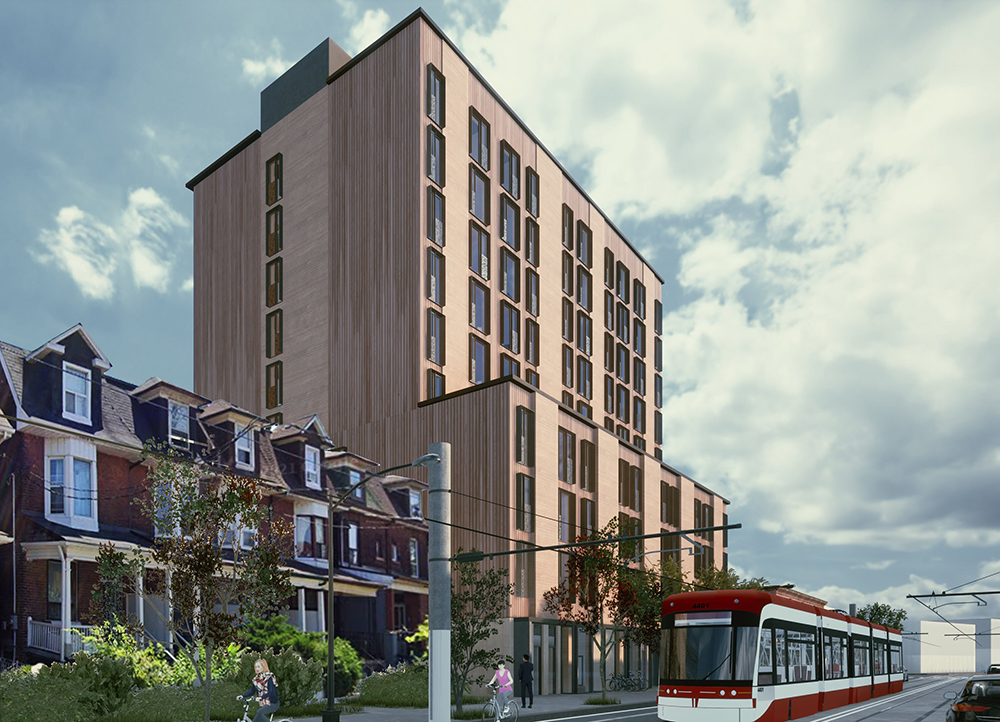
For Greener Buildings, We Need to Rethink How We Construct Them
To meet its pledge to be carbon neutral by 2050, Canada needs to cut emissions from the construction industry. Here’s how Read More
Concrete and steel are used in almost every building in Canada. These materials are relatively inexpensive and incredibly strong, but they have a hidden cost: a lot of carbon dioxide is emitted in producing them. About 13 per cent of the country’s annual carbon emissions are generated by the construction industry.
If Canada intends to meet its UN pledge to be carbon neutral by 2050, it will have to find a way to reduce the carbon emissions embodied in construction materials.
Using more organic substitutes, such as mass timber, is one answer. But Kelly Alvarez Doran, an adjunct professor at the Daniels Faculty of Architecture, Landscape, and Design, says Toronto needs to make several other changes as well, such as eliminating underground parking, ditching “stepbacks” and reducing average window-to-wall ratios.
Where construction materials are sourced is also crucial. Materials such as brick and aluminum require a lot of energy to produce; how this is generated has a major impact on a building’s embodied carbon. Doran recalls assessing a Toronto building that was clad in grey brick imported from Nebraska. Transporting the material here increased the embodied carbon by a few percentage points. But the state’s reliance on coal had a far larger impact, generating many times more carbon per brick than if the material had been made in Ontario, which relies mostly on nuclear and hydroelectric power.
Doran notes that to minimize a building’s lifetime environmental impact, architects must keep the impact of both embodied and operational carbon in mind. Triple-paned windows generate more carbon dioxide during construction, for example, but reduce emissions from heating and cooling over their lifespan.
In 2022, Doran and a former student, Juliette Cook, established Ha/f, a design consultancy that helps architectural firms with these complex assessments. The team is also collaborating with the City of Toronto on guidelines for reducing embodied carbon in the local construction industry. For Doran, the work has a deeply meaningful reward: “It’s how I address my anxiety about climate change.”
A Closer Look
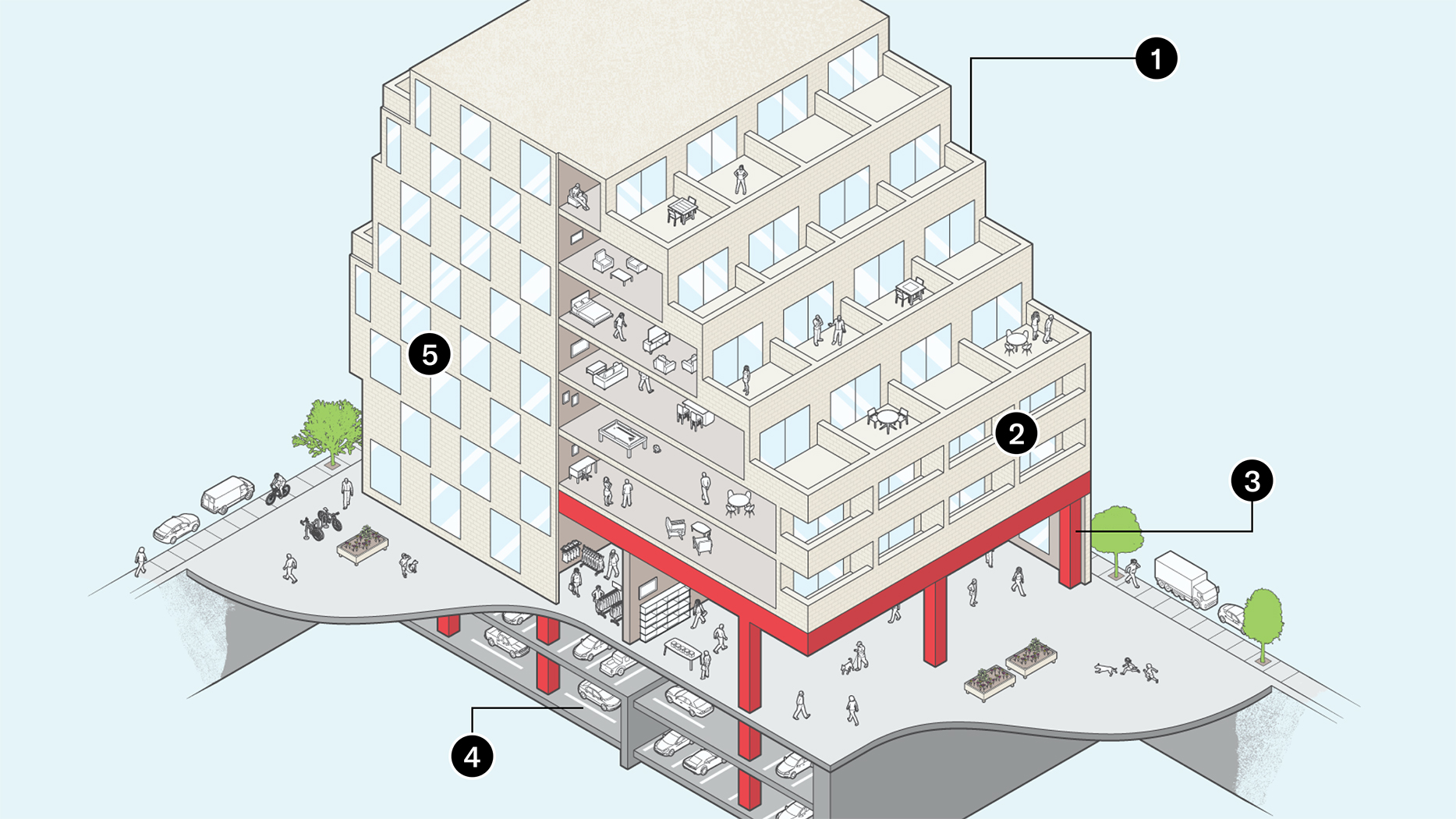
Each of the numbers in the illustration above match the cutaways below. Illustrations by Chris Philpot.

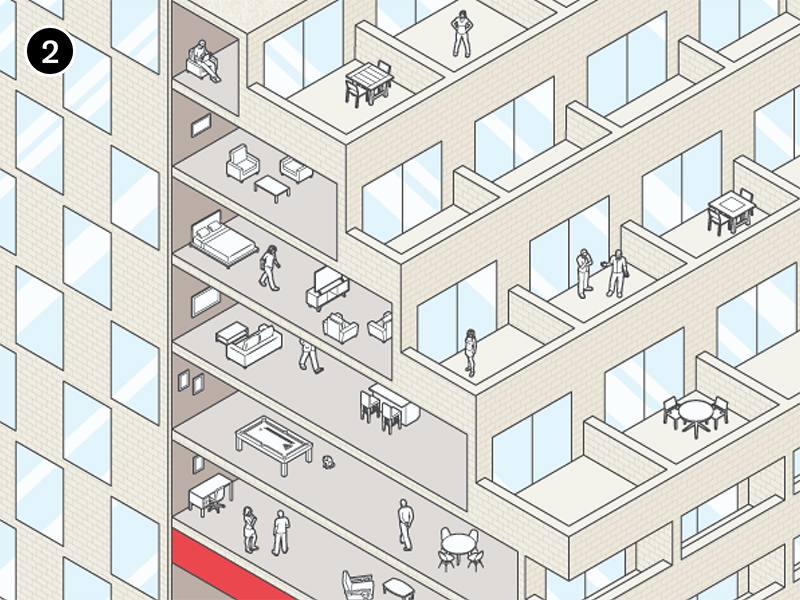
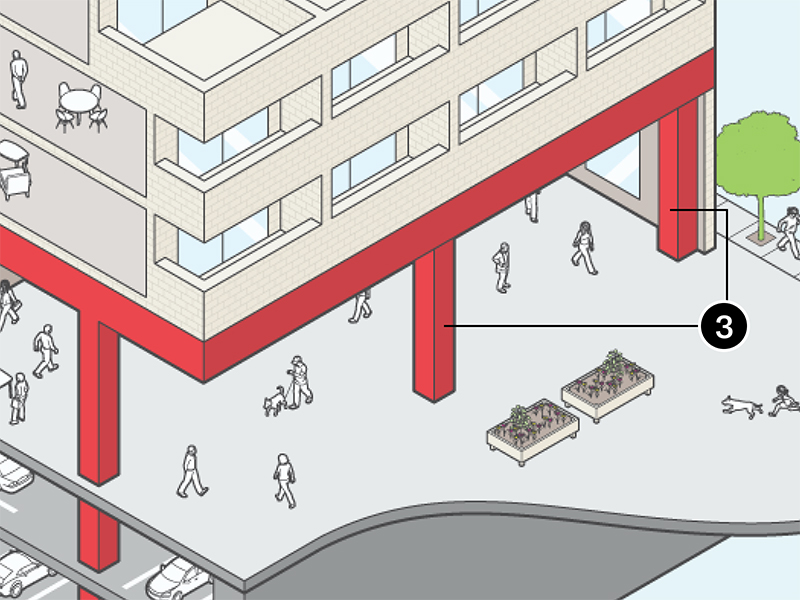
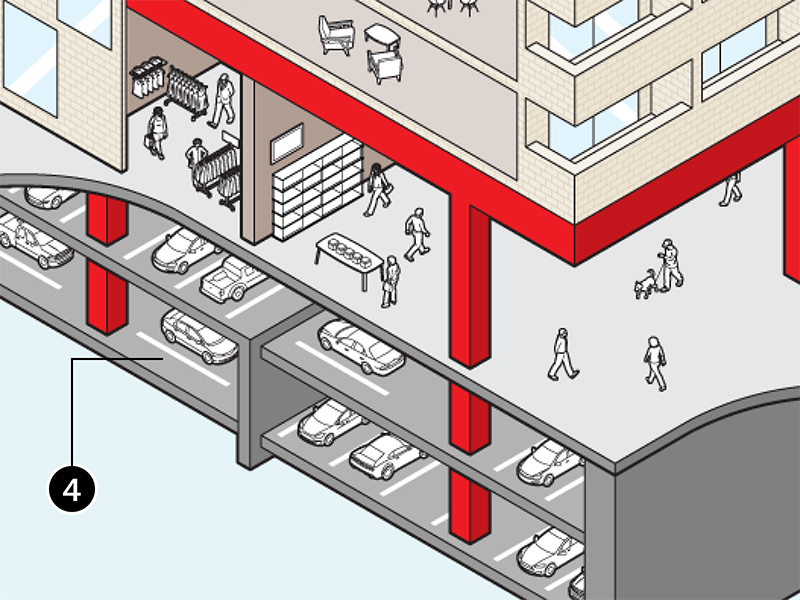
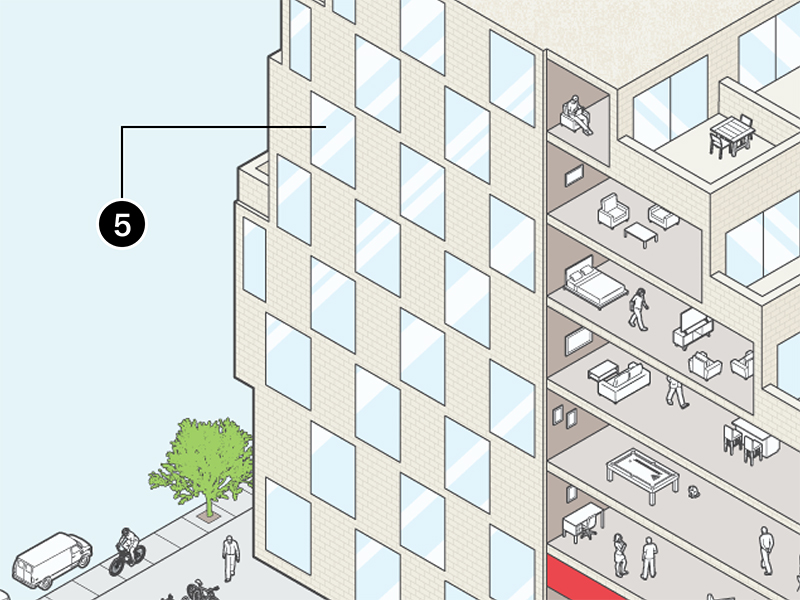
No Responses to “ For Greener Buildings, We Need to Rethink How We Construct Them ”
These are wonderful steps to reduce the carbon footprint of the construction industry. I do hope they are based on other factors as well, such as the location and climate of the building, the amount of daylight it receives, local flora and fauna, etc.
Having the community be a part of the process from the get-go, possibly through an "integrative" approach, would further benefit the long-term impact and usefulness of the building. Integrating biophilic design strategies for interior and exterior construction materials and looking at how to optimize the health of the building's users and the community would also help.
I'm looking forward to your ever-greener construction path!
Has anyone calculated the carbon cost of using mass timber, taking into consideration things like forest management, cutting down trees, trimming, hauling to mill, cutting to size, hauling to construction site, lifting into place. How does this compared to the use of steel and concrete? How do the labour costs compare: does one require more workers or more machinery?